Table of Contents
How Barometric Industrial Pressure Sensors are Used in Manufacturing Facilities
Barometric industrial pressure sensors are used in manufacturing facilities to monitor and control the pressure of gases and liquids. These sensors are used to ensure that the pressure in the facility is maintained at a safe level, and that any changes in pressure are detected and addressed quickly. For example, in a manufacturing facility that produces food products, barometric industrial pressure sensors are used to monitor the pressure of the air in the facility. If the pressure drops too low, it can cause the food products to spoil, so the sensors are used to detect any changes in pressure and alert the staff to take corrective action. In a manufacturing facility that produces chemicals, barometric industrial pressure sensors are used to monitor the pressure of the chemicals. If the pressure is too high, it can cause the chemicals to become unstable and potentially dangerous. The sensors are used to detect any changes in pressure and alert the staff to take corrective action.Measuring medium | Gases, vapours, liquids |
Inaccuracy | ±0.075% |
stability | ±0.1%/3 years |
The Benefits of Installing Barometric Industrial Pressure Sensors in a Factory Setting
Installing barometric industrial pressure sensors in a factory setting can be a great way to improve safety and efficiency. In one factory, the installation of these sensors allowed the staff to monitor the pressure of the air in the facility. This allowed them to quickly identify any changes in pressure that could indicate a potential safety hazard. The sensors also allowed the staff to monitor the pressure of the air in the facility in real-time. This allowed them to quickly identify any changes in pressure that could indicate a potential safety hazard. For example, if the pressure suddenly dropped, the staff could take action to prevent any potential accidents or injuries. The sensors also allowed the staff to monitor the pressure of the air in the facility in real-time. This allowed them to quickly identify any changes in pressure that could indicate a potential safety hazard. For example, if the pressure suddenly dropped, the staff could take action to prevent any potential accidents or injuries. In addition, the sensors allowed the staff to monitor the pressure of the air in the facility in real-time. This allowed them to quickly identify any changes in pressure that could indicate a potential safety hazard. For example, if the pressure suddenly dropped, the staff could take action to prevent any potential accidents or injuries.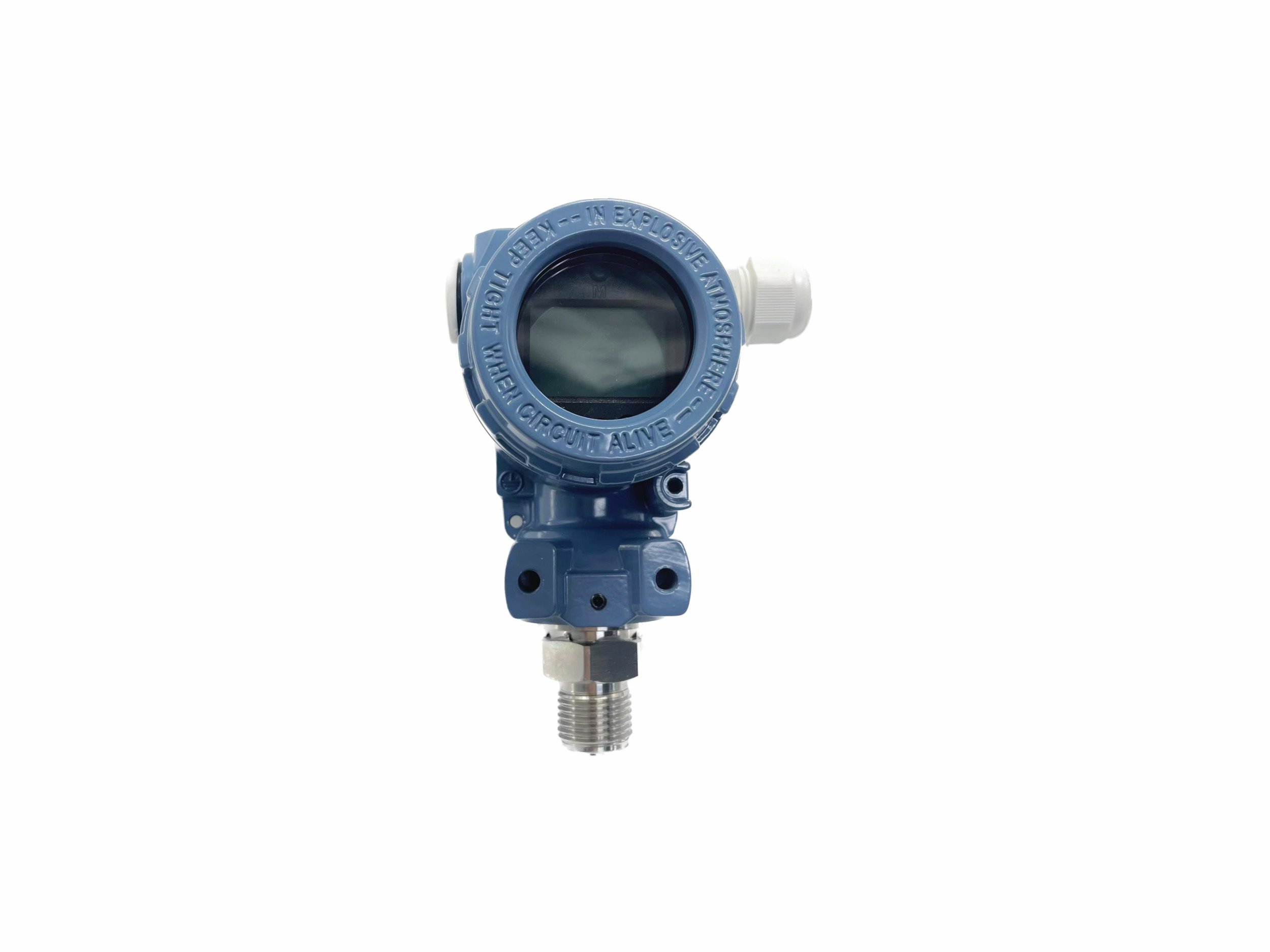