Table of Contents
Benefits of Regular Cleaning for Differential Pressure Sensors in Manufacturing Facilities
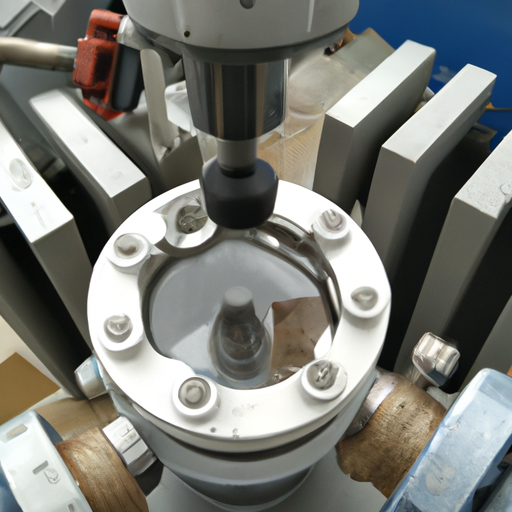
Differential pressure sensors play a crucial role in manufacturing facilities, helping to monitor and control pressure differentials in various processes. These sensors are essential for ensuring the efficiency and safety of operations in industries such as pharmaceuticals, food and beverage, and HVAC systems. However, like any other equipment, differential pressure sensors require regular maintenance to ensure accurate and reliable performance. One of the key maintenance tasks for differential pressure sensors is cleaning. Over time, these sensors can accumulate dust, dirt, and other contaminants that can affect their accuracy and performance. Regular cleaning of differential pressure sensors is essential to prevent issues such as clogging, drift, and inaccurate readings. By keeping these sensors clean, manufacturers can ensure that their processes run smoothly and efficiently. There are several benefits to regularly cleaning differential pressure sensors in manufacturing facilities. Firstly, cleaning helps to maintain the accuracy of the sensors. When sensors become dirty or clogged, they may not provide accurate readings, which can lead to errors in the manufacturing process. By cleaning the sensors regularly, manufacturers can ensure that they are providing reliable data for monitoring and control purposes. Secondly, cleaning differential pressure sensors can help to extend their lifespan. Contaminants such as dust and dirt can cause wear and tear on the sensors, leading to premature failure. By keeping the sensors clean, manufacturers can help to prolong their lifespan and reduce the need for costly replacements. Another benefit of regular cleaning is improved efficiency. Clean sensors are able to operate more effectively, providing accurate readings and helping to optimize processes. This can lead to increased productivity and cost savings for manufacturing facilities. In addition to these benefits, regular cleaning of differential pressure sensors can also help to ensure the safety of operations in manufacturing facilities. Accurate pressure readings are essential for maintaining safe working conditions and preventing accidents. By keeping the sensors clean and well-maintained, manufacturers can help to minimize the risk of safety incidents in their facilities.
Step-by-Step Guide to Properly Clean Differential Pressure Sensors in a Factory Setting
Differential pressure sensors are crucial components in many industrial processes, as they measure the difference in pressure between two points. Over time, these sensors can become dirty or clogged, leading to inaccurate readings and potential equipment malfunctions. Proper cleaning and maintenance of these sensors are essential to ensure their accuracy and longevity. Cleaning a differential pressure sensor in a factory setting requires careful attention to detail and adherence to specific procedures. In this step-by-step guide, we will outline the proper techniques for cleaning these sensors to maintain their optimal performance. The first step in cleaning a differential pressure sensor is to disconnect it from the system to prevent any damage or contamination. This may involve shutting off the power supply or isolating the sensor from the rest of the equipment. Once the sensor is safely disconnected, it can be removed from its mounting location for cleaning.Measuring medium | Gases, vapours, liquids |
Inaccuracy | ±0.075% |
stability | ±0.1%/3 years |