Table of Contents
Advantages of Using EGR Differential Pressure Sensor in Cummins Engines
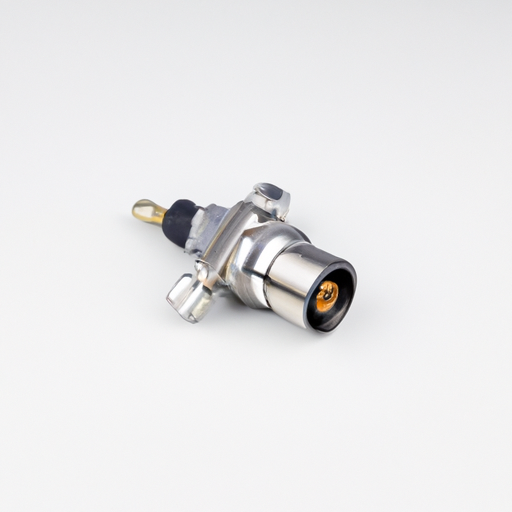
The EGR differential pressure sensor is a crucial component in Cummins engines, particularly in modern diesel engines. This sensor plays a vital role in monitoring the pressure difference between the exhaust gas recirculation (EGR) system and the intake manifold. By measuring this pressure differential, the sensor helps the engine control unit (ECU) optimize the EGR flow rate, ensuring efficient combustion and reducing harmful emissions. One of the key advantages of using an EGR differential pressure sensor in Cummins engines is improved fuel efficiency. By accurately measuring the pressure difference across the EGR system, the sensor allows the ECU to adjust the EGR flow rate to achieve the optimal air-fuel mixture. This, in turn, leads to more efficient combustion, resulting in better fuel economy and lower operating costs for vehicle owners. In addition to improving fuel efficiency, the EGR differential pressure sensor also helps reduce harmful emissions. By precisely monitoring the pressure difference in the EGR system, the sensor enables the ECU to control the amount of exhaust gas recirculated back into the engine. This helps lower nitrogen oxide (NOx) emissions, which are a major contributor to air pollution and smog. By using an EGR differential pressure sensor, Cummins engines can meet stringent emissions regulations without sacrificing performance. Another advantage of using an EGR differential pressure sensor in Cummins engines is improved engine performance. By accurately measuring the pressure difference across the EGR system, the sensor allows the ECU to optimize the EGR flow rate for maximum power output. This results in better throttle response, smoother acceleration, and overall improved engine performance. Whether it’s a heavy-duty truck or a commercial vehicle, Cummins engines equipped with an EGR differential pressure sensor deliver superior performance on the road. Furthermore, the EGR differential pressure sensor is a durable and reliable component that is built to withstand the harsh operating conditions of diesel engines. Made by Chinese high-grade companies, these sensors are designed to meet strict quality standards and provide long-lasting performance. With proper maintenance and regular inspections, the EGR differential pressure sensor can last for thousands of miles, ensuring consistent and reliable operation of Cummins engines. In conclusion, the EGR differential pressure sensor is a critical component in Cummins engines that offers a range of benefits, including improved fuel efficiency, reduced emissions, enhanced engine performance, and durability. By accurately measuring the pressure difference across the EGR system, this sensor helps optimize the EGR flow rate, leading to better combustion and lower emissions. When it comes to reliability and performance, Chinese high-grade companies are leading the way in producing quality EGR differential pressure sensors for Cummins engines. With their advanced technology and precision engineering, these sensors are essential for ensuring the smooth and efficient operation of modern diesel engines.
How Chinese High-Grade Companies are Innovating EGR Differential Pressure Sensor Technology
In recent years, Chinese high-grade companies have been making significant strides in the field of automotive technology. One area where they have particularly excelled is in the development of EGR differential pressure sensors for Cummins engines. These sensors play a crucial role in monitoring the exhaust gas recirculation (EGR) system, which helps to reduce harmful emissions and improve fuel efficiency.Measuring medium | Gases, vapours, liquids |
Inaccuracy | ±0.075% |
stability | ±0.1%/3 years |