Understanding the Principle of Pressure Transducers: A Comprehensive Guide

Understanding the Principle of Pressure Transducers: A Comprehensive Guide
Measuring medium | Gases, vapours, liquids |
Inaccuracy | ±0.075% |
stability | ±0.1%/3 years |
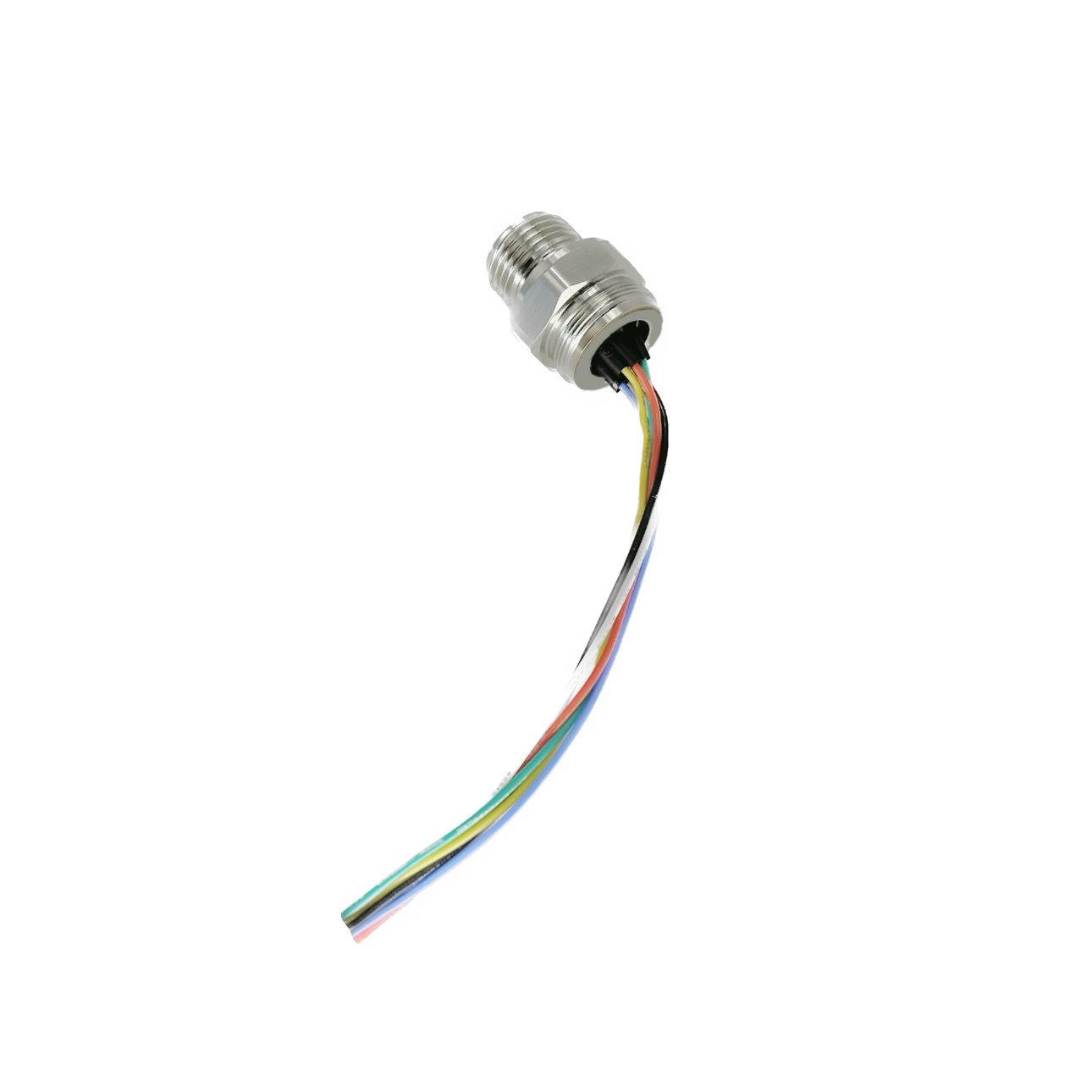
Measuring medium | Gases, vapours, liquids |
Inaccuracy | ±0.075% |
stability | ±0.1%/3 years |
Exploring the Benefits of Purchasing Pressure Transmitters from Siemens Chinese Wholesalers Are you looking for reliable pressure transmitters for your business? If so, you should consider purchasing from Siemens Chinese wholesalers. Siemens is a trusted name in the industry, and their Chinese wholesalers offer a variety of benefits that make them a great choice for…
Understanding the Operating Principle of Pressure Transmitters in Chinese High-Grade Factories Pressure transmitters are essential components in various industrial processes, providing accurate and reliable measurements of pressure levels. In Chinese high-grade factories, these devices play a crucial role in ensuring the efficiency and safety of operations. Understanding the working principle of pressure transmitters is key…
Benefits of Pressure Transmitter Calibration Pressure transmitter calibration is a crucial process in ensuring the accuracy and reliability of pressure measurement instruments. In industries such as manufacturing, oil and gas, and pharmaceuticals, pressure transmitters play a vital role in monitoring and controlling various processes. To maintain the efficiency and safety of these processes, it is…
Differential Pressure Sensor Installation Supplier: How to Choose the Right One for Your Needs When selecting a differential pressure sensor installation supplier, it is important to consider a number of factors. First, it is important to consider the type of application for which the sensor will be used. Differential pressure sensors are used in a…
Benefits of Pressure Transmitter Calibration Pressure transmitter calibration is a critical process in ensuring the accuracy and reliability of pressure measurement instruments. By calibrating pressure transmitters, manufacturers can verify that the devices are operating within specified tolerances and are providing accurate readings. One of the most common methods of calibrating pressure transmitters is using a…
Benefits of Using a Differential Pressure Sensor for DPF Systems Differential pressure sensors play a crucial role in diesel particulate filter (DPF) systems, helping to monitor and control the efficiency of the filter. In recent years, Chinese manufacturers have emerged as leaders in producing high-quality differential pressure sensors for DPF systems. These sensors offer a…