Introduction to Pressure Transducer Types in Factory Settings
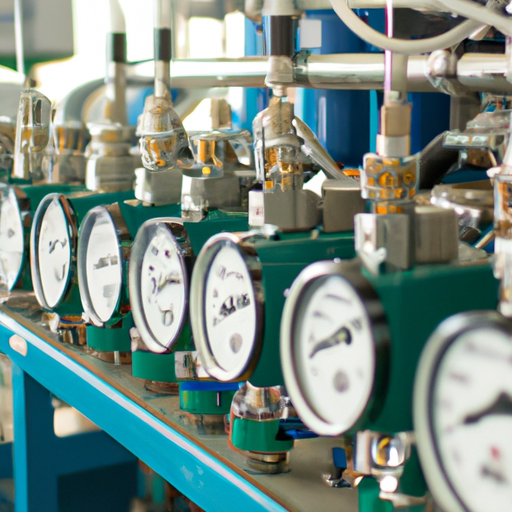
Pressure Transducer Types in Factory Settings
Measuring medium | Gases, vapours, liquids |
Inaccuracy | ±0.075% |
stability | ±0.1%/3 years |
Measuring medium | Gases, vapours, liquids |
Inaccuracy | ±0.075% |
stability | ±0.1%/3 years |
Different Types of Pressure Transmitters Pressure transmitters are essential devices used in various industries to measure and monitor pressure levels in different systems. These devices play a crucial role in ensuring the safety and efficiency of processes by providing accurate and reliable pressure readings. In China, there are several companies that manufacture high-quality pressure transmitters,…
Exploring the Benefits of Pressure Transmitter vs Pressure Transducer Factory Solutions When it comes to measuring pressure, two of the most popular solutions are pressure transmitters and pressure transducers. Both of these solutions offer a range of benefits, but which one is right for your factory? Let’s explore the advantages of each to help you…
Exploring the Benefits of Pressure Transmitters from China’s Top Manufacturers China is home to some of the world’s top pressure transmitter manufacturers, offering a wide range of products that can be used in a variety of industrial and commercial applications. Pressure transmitters are devices that measure and transmit pressure readings to a remote location, allowing…
The Importance of Pressure Transducer Sensors in Industrial Applications Pressure transducer sensors play a crucial role in various industrial applications. These sensors are designed to measure and monitor pressure levels in different systems, providing valuable data that helps ensure the smooth operation and safety of industrial processes. In recent years, Chinese manufacturers have emerged as…
How to Choose the Right Pressure Transmitter Supplier for Your Business Choosing the right pressure transmitter supplier for your business is an important decision that can have a lasting impact on your success. It’s essential to find a supplier that can provide you with reliable, high-quality products and services that meet your needs. Here are…
The Impact of Price on Pressure Sensor Companies: How to Stay Competitive in a Changing Market The pressure sensor market is a highly competitive and ever-changing landscape. Companies must stay ahead of the curve in order to remain competitive and profitable. Price is one of the most important factors in the pressure sensor market, and…