Table of Contents
Benefits of Using Differential Pressure Sensors in Chilled Water Systems
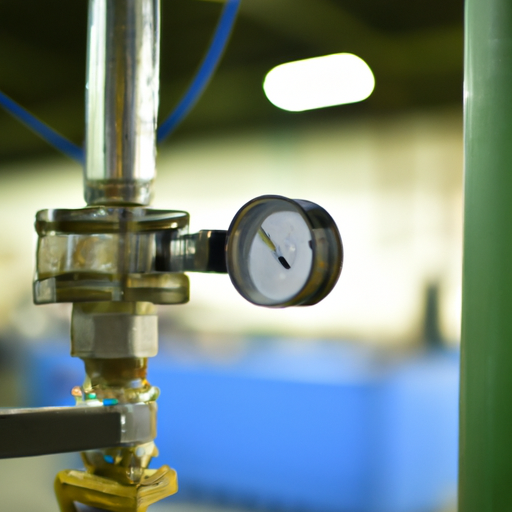
Differential pressure sensors play a crucial role in maintaining the efficiency and performance of chilled water systems. These sensors are designed to measure the difference in pressure between two points in a system, providing valuable data that can be used to optimize the system’s operation. In a chilled water system, differential pressure sensors are typically used to monitor the pressure drop across filters, pumps, and other components, helping to ensure that the system is operating at peak efficiency. One of the key benefits of using differential pressure sensors in chilled water systems is improved energy efficiency. By monitoring the pressure drop across key components, such as filters and pumps, operators can identify potential issues that may be causing the system to work harder than necessary. This allows for timely maintenance and adjustments to be made, helping to reduce energy consumption and lower operating costs. In addition to improving energy efficiency, differential pressure sensors can also help to extend the lifespan of equipment in chilled water systems. By monitoring pressure drops and identifying issues early on, operators can address potential problems before they escalate and cause damage to critical components. This proactive approach to maintenance can help to prevent costly repairs and downtime, ultimately prolonging the life of the system as a whole. Another benefit of using differential pressure sensors in chilled water systems is improved system performance. By continuously monitoring pressure differentials, operators can ensure that the system is operating within optimal parameters. This can help to prevent issues such as low flow rates, air pockets, and pump cavitation, all of which can negatively impact the performance of the system. By maintaining proper pressure differentials, operators can ensure that the system is able to deliver the required cooling capacity consistently and efficiently. Furthermore, differential pressure sensors can also help to improve the overall reliability of chilled water systems. By providing real-time data on pressure differentials, operators can quickly identify and address any issues that may arise, minimizing the risk of system failures and downtime. This proactive approach to maintenance can help to ensure that the system is able to operate reliably and consistently, meeting the cooling needs of the facility without interruption. Overall, the benefits of using differential pressure sensors in chilled water systems are clear. From improved energy efficiency and extended equipment lifespan to enhanced system performance and reliability, these sensors play a critical role in optimizing the operation of chilled water systems. By investing in differential pressure sensors from a reputable manufacturer, operators can ensure that their systems are able to operate at peak efficiency and performance, ultimately saving time and money in the long run.
How to Choose the Right Differential Pressure Sensor for Your Chilled Water System Manufacturing Process
When it comes to manufacturing chilled water systems, one of the key components that plays a crucial role in ensuring efficient operation is the differential pressure sensor. This sensor is responsible for measuring the pressure difference between two points in the system, providing valuable data that can help optimize performance and prevent potential issues. Choosing the right differential pressure sensor for your chilled water system manufacturing process is essential to ensure accurate and reliable measurements. There are several factors to consider when selecting a sensor, including the type of sensor, the range of pressure it can measure, and the accuracy of the readings it provides. One of the first things to consider when choosing a differential pressure sensor is the type of sensor that best suits your needs. There are several types of sensors available, including diaphragm, bourdon tube, and capacitive sensors. Each type has its own advantages and disadvantages, so it’s important to carefully evaluate your requirements before making a decision. Another important factor to consider is the range of pressure that the sensor can measure. Different chilled water systems operate at different pressure levels, so it’s crucial to choose a sensor that can accurately measure the pressure range of your system. Selecting a sensor with a wider range of pressure capabilities can provide more flexibility and ensure that it can handle any fluctuations in pressure that may occur.Measuring medium | Gases, vapours, liquids |
Inaccuracy | ±0.075% |
stability | ±0.1%/3 years |